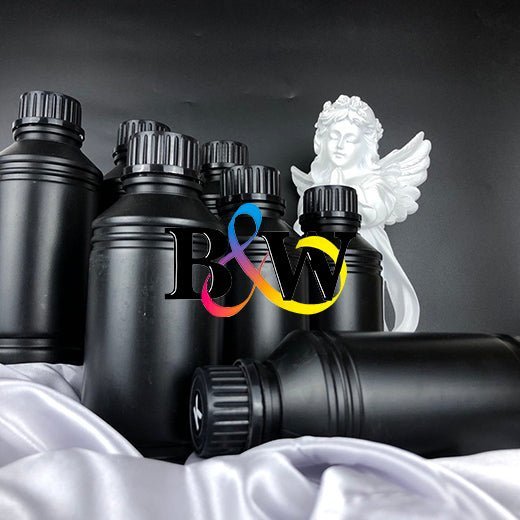
How UV Ink Dyes Fabrics
Compartir
UV ink dyeing technology, particularly for fabric applications, combines modern inkjet printing with ultraviolet (UV) light curing principles to achieve efficient, precise, and environmentally friendly dyeing results.
Composition and Characteristics of UV Ink
Pigments or Dyes: These provide the color components, typically using high-concentration pigments to ensure vibrant color effects.
Photoinitiators: When exposed to ultraviolet light, photoinitiators undergo a chemical reaction, causing the ink's resin to quickly solidify.
Resins: These form a strong layer on the fabric surface, enhancing the ink's adhesion and durability.
Solvents: These adjust the viscosity of the ink to ensure its flowability and adaptability.
Compared to traditional water-based or oil-based inks, the main feature of UV ink is its ability to quickly cure under UV light without relying on heat or moisture from the air, making the curing process highly efficient.
Dyeing Principles and Process Flow
Ink Application (Printing or Coating)
The UV ink is applied to the fabric surface using inkjet printing technology. With high-precision inkjet equipment, the ink can be evenly sprayed to create patterns, text, or full-color dyeing. This method is ideal for high-precision customized dyeing, such as personalized clothing or small-batch fabric production. Alternatively, coating techniques can be used to evenly apply the ink directly onto the fabric.
UV Curing
After the UV ink is applied to the fabric surface, the next step is the UV curing process. UV lamps (typically ultraviolet tube lights or LED lights) are used to expose the fabric, and the photoinitiators trigger a reaction, causing the resin in the ink to polymerize, turning it from liquid to solid. The curing process is extremely rapid, typically completed within seconds, making it much more efficient than traditional heat curing or air-drying methods.
Post-treatment of Finished Products
After UV curing, the fabric's dye is firmly set. At this point, the colors are vibrant and durable. The dyed fabric may undergo further post-treatment processes, such as washing or softening, to improve comfort and durability.
Advantages of UV Ink Dyeing
Efficient Curing: The UV curing process is extremely fast, significantly boosting production efficiency. The curing time is reduced to just a few seconds, compared to traditional dyeing methods.
Vivid Color: The high concentration of pigments and dyes in UV inks results in bright, stable colors, especially suited for detailed patterns.
Environmentally Friendly: UV inks do not contain solvents or other harmful substances, and the curing process does not emit harmful gases, making it more environmentally friendly than traditional dyes and inks.
Low Energy Consumption: UV curing consumes less energy compared to traditional heat curing methods, meeting energy-saving and environmental requirements for production.
No Heat Treatment Required: Traditional dyeing processes often require high temperatures, while UV ink curing does not require heating, preventing potential damage to fabrics from high temperatures.
Limitations of UV Ink Dyeing
Limited Fabric Compatibility: While UV inks can be applied to various textiles, their compatibility with certain materials may be limited. For example, fabrics with high absorbency or smooth surfaces may require special pre-treatment or modified ink formulations.
Washing Durability Issues: Although UV ink is durable after curing, the washfastness and friction resistance of dyed fabrics may still need improvement. Under conditions of high-temperature washing or prolonged abrasion, colors may fade or peel.
Higher Costs: The cost of UV ink, equipment, and curing devices is relatively high, which makes the technology more expensive for large-scale production, limiting its use in low-cost, mass-production settings.
UV Ink Dyeing Application Scenarios
Customized Apparel: Ideal for custom-made T-shirts, sportswear, workwear, etc., capable of printing complex patterns to meet personalized needs.
Textile Printing: Suitable for high-precision fabric printing, especially for intricate designs and small-batch customization.
Advertising Banners and Display Materials: Used in the advertising industry for fabric displays, tents, signage, and other large-format printing needs.
Special Fabrics: Applied to high-end home décor fabrics, curtains, tablecloths, etc., providing high-quality dyeing effects.