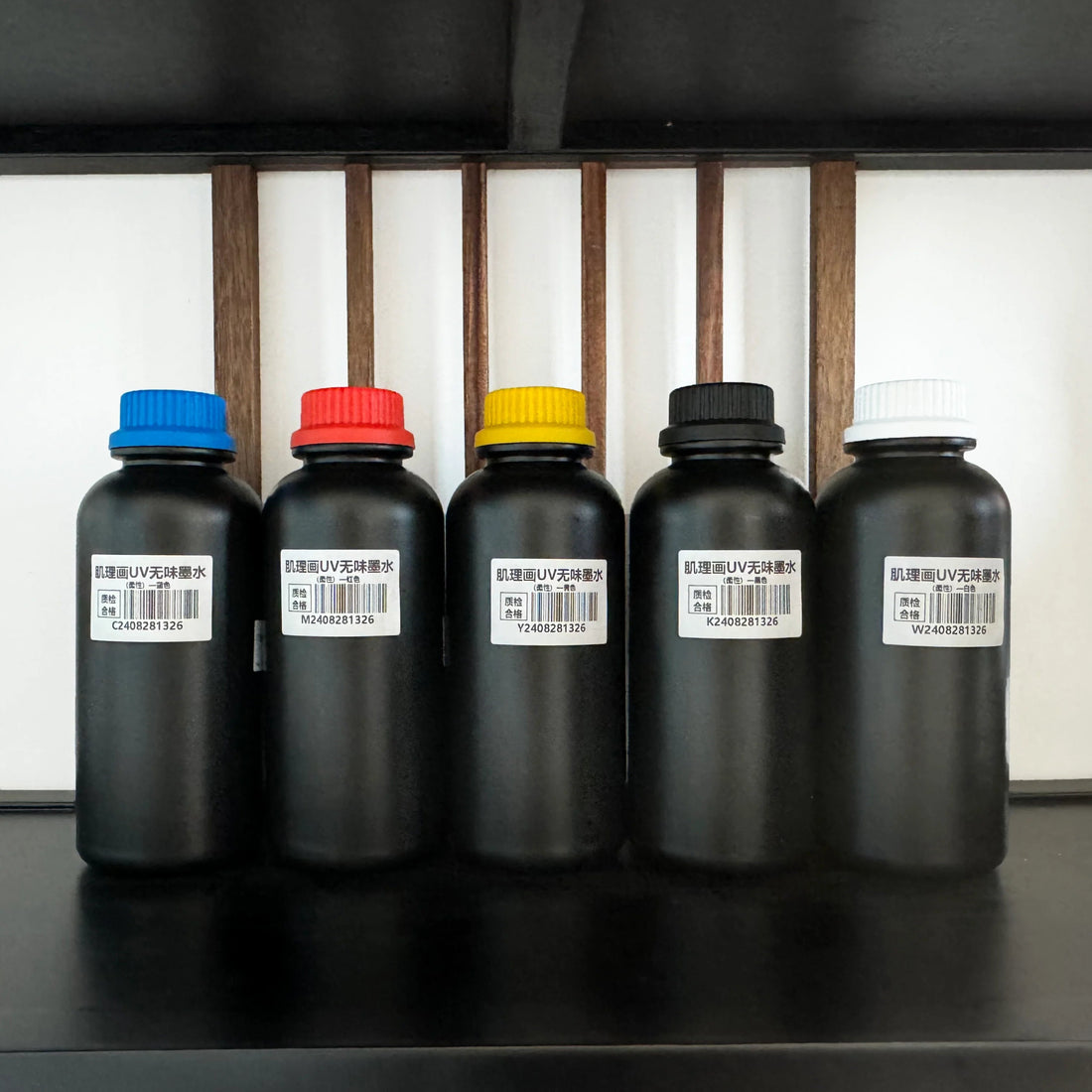
Ink Basics
Share
Ink, as a core component of modern printing and writing tools, is widely used in inkjet printers, laser printers, and various forms of manual artwork. Different types of ink vary significantly in technology, physical properties, and application scenarios. Understanding the classification of ink, key performance indicators, and maintenance requirements is crucial for selecting the right ink and extending the lifespan of printing devices. This article will explore the basic knowledge of ink in detail, covering aspects such as classification, key performance parameters, and maintenance requirements, providing professionals with a comprehensive understanding of the field.
Classification of Ink
There are numerous types of ink, typically classified according to the colorant composition and solvent type. These classification methods help us understand the basic properties of ink and guide appropriate selection for various applications.
A. Based on Colorant
-
Dye-based Ink:
- Basic Principle: Dye-based ink uses water-soluble dyes as colorants, which dissolve in the liquid and directly bond with the paper's surface. Since dyes are molecular-level dissolved substances, they can provide bright and transparent colors.
- Advantages: High color saturation, ideal for printing detailed images and photos, and relatively low cost.
- Disadvantages: Poor lightfastness, susceptible to fading under UV light; poor water resistance, easily damaged by moisture; limited applicability, particularly in outdoor or high-humidity environments.
-
Pigment-based Ink:
- Basic Principle: Pigment-based ink uses small pigment particles instead of soluble dyes. The pigment particles do not dissolve in the solvent and remain suspended in the liquid, adhering to the paper’s surface, providing opaque colors.
- Advantages: Excellent lightfastness, water resistance, and abrasion resistance, making it suitable for art prints, archival documents, photo printing, and other high-demand applications.
- Disadvantages: Lower color saturation compared to dye-based inks; the printing result may appear less vibrant; pigment sedimentation can occur, affecting print quality, particularly on low-quality paper.
B. Based on Solvent
-
Water-based Ink:
- Basic Principle: Water-based ink uses water as the main solvent, combined with water-soluble dyes or pigments as colorants. It is characterized by being environmentally friendly, with low volatility, and is suitable for a wide range of printing applications.
- Advantages: Non-toxic, environmentally friendly, and dries at a moderate speed, making it suitable for home and office environments. It flows well, providing smooth prints on a variety of paper surfaces.
- Disadvantages: Susceptible to moisture; in high-humidity environments, color changes or printhead blockages may occur. Its long-term durability is also limited.
-
Oil-based Ink:
- Basic Principle: Oil-based ink uses mineral or vegetable oils as the main solvent, with pigments or dyes suspended in the liquid. Oil-based inks offer better solubility and stability, often used in industrial applications with high printing demands.
- Advantages: Strong water resistance, fast drying speed, and suitability for outdoor environments and industrial printing. It can print on various substrates, including paper, plastic, and metal.
- Disadvantages: Due to its strong solvent volatility, it has a strong odor, requiring good ventilation. It also places higher demands on printing equipment.
Key Performance Parameters of Ink
The physical and chemical properties of ink directly affect its print quality, printer performance, and maintenance needs. The following are key performance parameters that significantly impact ink’s flow, printing precision, and the long-term stability of devices.
A. Viscosity and Surface Tension
-
Viscosity: Viscosity is the resistance of a liquid to flow. High viscosity can cause ink to flow poorly, affecting printhead performance and print speed. On the other hand, too low a viscosity can result in unstable ink drops, causing poor print quality.
- Requirement: Inkjet printer ink typically requires a lower viscosity (around 2-5 centipoise) to ensure smooth flow and stable jetting.
-
Surface Tension: Surface tension determines how well the ink adheres to the surface of the paper. Higher surface tension helps maintain stable ink drop formation during printing, preventing excessive spreading or layering of the ink.
- Requirement: To ensure accurate and fine ink drop formation, inkjet ink typically requires a high surface tension (usually in the range of 30-50 mN/m).
B. pH Value
The pH value measures the acidity or alkalinity of a liquid. If the pH is too low or too high, it can corrode the printhead or cause blockages. To avoid damaging the printhead and ensure good adhesion of the ink to the paper, the pH value of ink should generally remain in the neutral to mildly alkaline range, typically around 7-8.
- Requirement: The pH value of ink should be strictly controlled between 7 and 12 to avoid acidic or alkaline environments that could affect the performance of the equipment.
C. Conductivity
Conductivity measures the strength of a solution’s ability to conduct electricity and is typically related to the amount of dissolved salts in the ink. Excessive salts can lead to printhead crystallization or electrochemical corrosion, which may cause printing malfunctions.
- Requirement: The ideal conductivity should be kept low (generally below 0.5%), to prevent crystallization in the printhead and ensure stable jetting performance.
D. Dispersants and Wetting Agents
Dispersants and wetting agents are surfactants that improve the ink’s affinity for the paper and printhead surfaces. These additives prevent pigment particles or dye molecules from precipitating, ensuring even dispersion of the ink and reducing blockages and impurities during printing.
- Requirement: The dispersant must effectively keep the pigment particles suspended, avoiding sedimentation and improving the ink’s stability and flow during printing.
Ink Maintenance and Storage
The quality of ink can be influenced by storage conditions, and proper storage methods can significantly extend its shelf life and maintain its performance. Ink typically has a shelf life of around 2 years, but specific storage conditions can affect its degradation rate.
A. Storage Environment
- Temperature Control: Ink should be stored in a cool, dry environment, avoiding exposure to high or low temperatures. Ideal storage temperatures are typically between 10°C and 25°C. Excessive heat may cause solvent evaporation and ink drying, while extremely low temperatures may cause ink to freeze or separate.
- Avoid Direct Sunlight: UV rays in direct sunlight can degrade dye molecules, causing ink to fade or lose quality. Therefore, ink should be stored away from direct sunlight to prevent UV damage.
B. Sealed Storage
Ink bottles should be tightly sealed to prevent moisture and air from entering, which could cause the ink to dry out, form clumps, or separate. Sealing helps to extend the ink's shelf life and maintain its quality.
C. Avoid Mixing Different Inks
Different types of ink (e.g., dye-based vs. pigment-based) should not be mixed in the same printer, as this can cause blockages, degrade print quality, and even damage the device.
Ink, as a core material in modern printing technology, comes in a variety of types with significant differences in properties and applications. Through an in-depth understanding of ink classification and its physical and chemical properties, we can not only select the most appropriate ink type for our needs but also maintain the ink properly to extend the lifespan of our devices and improve print quality. Whether in home use, commercial printing, or artistic creation, choosing the right ink and ensuring proper maintenance is crucial to achieving optimal results.