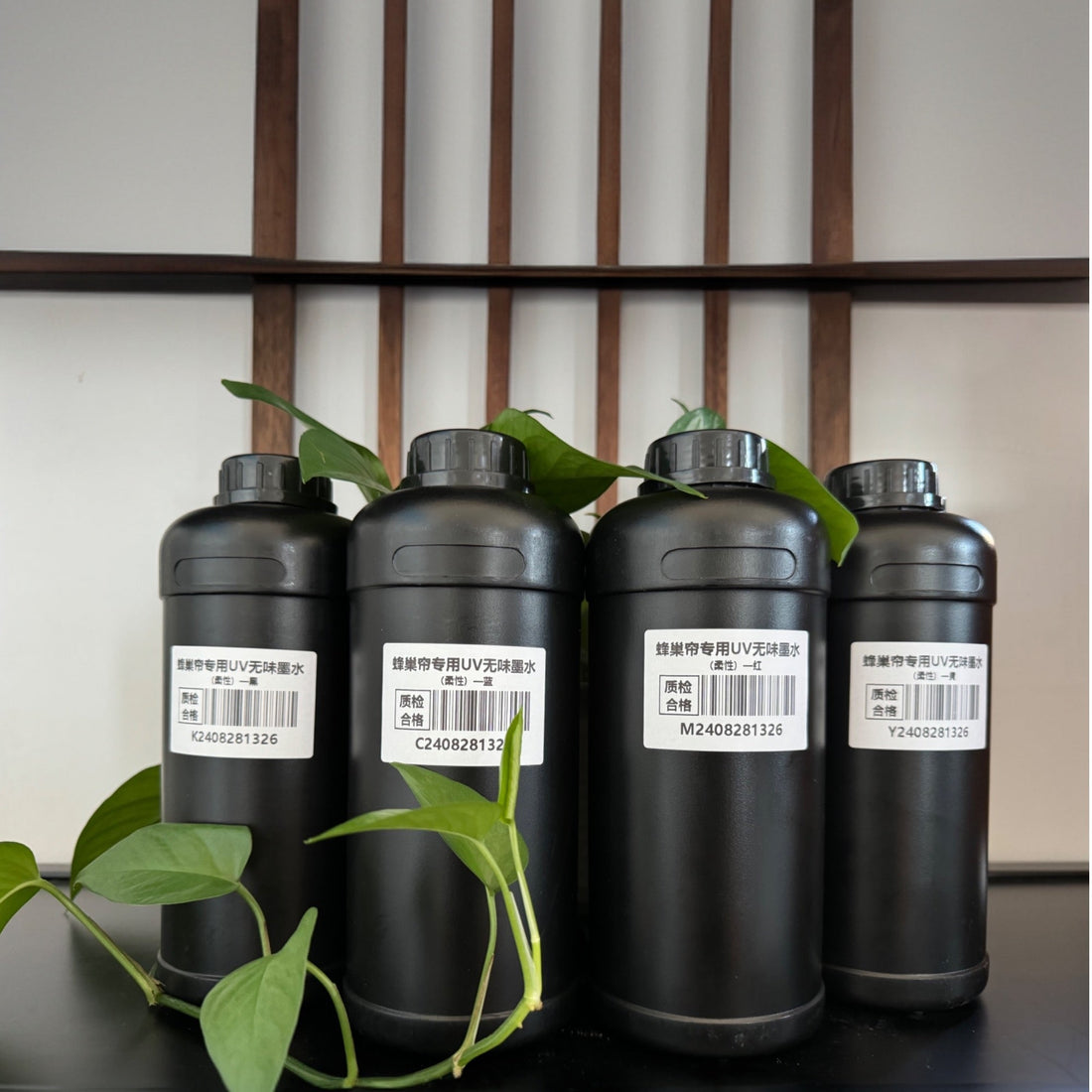
How to Improve the Adhesion of UV Ink
Share
Improving the adhesion of UV ink depends on optimizing and controlling multiple factors, including ink formulation, substrate surface treatment, UV curing process, and environmental conditions. To achieve strong bonding between the ink and the substrate surface, a systematic improvement of each link is necessary. Below is a professional analysis of how to improve the adhesion of UV ink:
Ink Formulation Design
A well-designed ink formulation is the foundation for enhancing the adhesion of UV ink. Key components include resins, pigments, photoinitiators, and solvents. The appropriate resin system and formulation design must be chosen according to the substrate type and usage requirements.
Resin Selection: Resins are one of the most critical components in UV ink, and different types of resins have significantly different impacts on adhesion.
Acrylic Resin: Known for excellent adhesion, especially suitable for low surface energy substrates like plastics and paper.
Polyurethane Resin: Offers better flexibility and abrasion resistance, ideal for printing on metals, paper, and textiles.
Epoxy Resin: Provides strong adhesion, especially suitable for high surface energy materials like metals and glass.
Silane-modified Resin: Used to increase surface activity and enhance adhesion to various substrates.
Additives and Enhancers: Additives such as tackifiers, toughening agents, and crosslinkers can improve resin adhesion and durability. Crosslinkers promote the formation of a more durable adhesive film by initiating crosslinking reactions between resin molecules during curing, significantly enhancing adhesion.
Substrate Surface Treatment
The surface energy and roughness of the substrate are decisive factors influencing UV ink adhesion. To enhance ink adhesion, the substrate typically needs surface pretreatment.
Surface Activation Treatment: Low surface energy materials (e.g., PE, PP, PET plastics) can be treated with methods such as plasma treatment, flame treatment, or laser treatment to effectively increase the surface energy and improve ink wetting and adhesion. Plasma treatment uses high-frequency electric fields to excite gas molecules, generating ions and free radicals, which produce polar groups on the substrate surface, thus improving ink adhesion.
Chemical Treatment: Certain chemicals can be used for surface coating or reactive treatment, which effectively increases surface roughness or forms chemical bonds on the substrate surface to enhance ink adhesion. For metals and glass, treatments such as phosphating or anodizing can significantly improve ink adhesion.
Mechanical Roughening: Methods such as sandblasting or mechanical polishing can increase the surface roughness, enhancing the mechanical adhesion of the ink. This is particularly effective for metals and hard substrates.
UV Curing Process Optimization
The curing process of UV ink directly impacts its adhesion. Incomplete or excessive curing can negatively affect ink performance, especially adhesion. Therefore, it is essential to carefully control the UV curing process parameters.
UV Irradiation Intensity and Wavelength: The power and wavelength of the UV lamp significantly impact curing performance. Different ink systems absorb UV light at different wavelengths, so selecting the appropriate UV light source (such as Hg lamps or LED lamps) can significantly improve curing efficiency.
Curing Time and Light Source Distance: Insufficient curing time or excessive distance between the light source and the substrate can result in incomplete curing, affecting adhesion. Typically, UV ink must be cured at an appropriate irradiation intensity and time to ensure that the resin molecules form a stable crosslinked structure.
Curing Uniformity: UV curing requires uniform exposure to light across the entire printing surface. Uneven curing can lead to areas with insufficient curing, affecting the stability of the adhesion. Modern UV printing equipment is typically equipped with efficient light source layouts and intensity adjustment systems to ensure uniform curing.
Environmental Factors Control
The adhesion of UV ink is influenced not only by the ink formulation and substrate surface treatment but also by environmental factors such as temperature and humidity. Ensuring optimal environmental conditions can help improve ink adhesion.
Temperature and Humidity Control: Excessive temperatures or humidity can affect the rheology and curing performance of the ink. High humidity may lead to moisture absorption or incomplete curing, reducing adhesion. Typically, the optimal curing temperature for UV inks is between 20°C and 30°C, and the humidity should be controlled between 40% and 60%.
Airflow and Dust Control: Proper airflow during UV curing helps solvent evaporation and prevents dust contamination of the curing layer. Dust adhering to the ink surface can affect the smoothness and adhesion of the ink. Therefore, controlling cleanliness and airflow in the production environment is critical.
Printing Process Selection and Optimization
Different printing processes have varying requirements and impacts on ink adhesion. Selecting the appropriate printing method and process parameters is crucial for different printing needs.
Flexographic Printing: Flexographic printing ensures uniform ink coating and high adhesion, especially for complex patterns and fine fonts, making it ideal for substrates like plastic films and paper.
Screen Printing: Screen printing can apply thicker ink layers and is suitable for rougher surfaces that require strong adhesion, such as wood, glass, and metal.
Direct and Indirect Coating: For certain high-demand prints, multiple coating or priming processes can be used. A primer layer can enhance ink adhesion, especially on metals or low surface energy materials, providing a stronger adhesive foundation.
Special Treatments and Post-Protection
For certain special applications, additional measures may be needed after printing to improve ink adhesion and durability.
Coating and Sealing: For printed products subject to wear or scratching, a protective coating such as a clear coat or varnish can be applied. This protective layer not only enhances ink adhesion but also increases the ink surface’s abrasion resistance and aging resistance.
Durability Testing: Products can be subjected to friction, aging, and chemical solvent tests to verify the stability and longevity of ink adhesion. For high-end or special applications, a dual-curing technique, combining UV curing and thermal curing, may be used to enhance the overall performance of the ink.
Improving the adhesion of UV ink is a multifaceted technical issue that requires optimization and control across several dimensions, including ink formulation, substrate surface treatment, UV curing process, environmental conditions, and printing processes. By carefully selecting resin types, optimizing surface treatment processes, accurately controlling UV curing conditions, and ensuring a stable production environment, high adhesion can be achieved on various substrates, enhancing printing quality and the product’s lifespan.