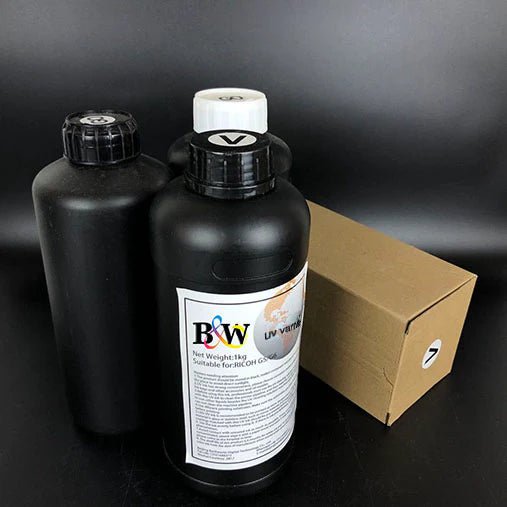
How To Improve Uv Ink Adhesion
Share
Improving UV ink adhesion is essential for ensuring high-quality prints, particularly in applications such as packaging, labels, and other substrates. Poor adhesion can lead to issues like smudging, scratching, or peeling. There are several strategies you can implement to enhance UV ink adhesion, depending on the type of substrate, ink, and printing process you are using.
1. Surface Preparation
- Clean the substrate: Ensure that the surface of the material is free of dirt, oil, dust, or any contaminants. A clean surface provides better adhesion for the UV ink.
- Use surface primers: Primers can help increase the ink's bond with substrates that are typically difficult to print on, such as plastic or metal. They create a better mechanical bond between the ink and the substrate.
- Etching or corona treatment: For plastic or non-porous substrates, processes like corona discharge treatment or plasma treatment can increase the surface energy, which improves ink adhesion by making the surface more receptive to the ink. These treatments modify the surface of the substrate on a molecular level to promote better adhesion.
- Chemical adhesion promoters: Some surfaces, particularly plastics, may benefit from using adhesion promoters or bonding agents that are applied before printing.
2. Substrate Selection
- Choose the right material: Certain materials are more suited to UV ink adhesion. For example, coated papers, some plastics (like polypropylene or PET), and metals may need specific inks or treatments to ensure proper bonding. Ensure that your substrate is compatible with the ink being used.
- Proper substrate coating: Coated substrates (e.g., papers with a special finish) may already provide better adhesion for UV inks. Uncoated substrates may need additional treatment or the use of specialized UV inks designed for uncoated or porous materials.
3. Ink Formulation
- Use the right UV ink for the substrate: UV inks come in different formulations (e.g., UV curable, UV flexo, UV offset). Using the correct type of UV ink based on the substrate's characteristics is crucial. Some UV inks are formulated to adhere better to specific substrates.
- Ink viscosity: Make sure the viscosity of the UV ink is appropriate for the printing process (e.g., screen printing, flexography, offset). Thicker inks might have trouble adhering well, while overly thin inks could lead to poor coverage and adhesion.
- Ink curing properties: Ensure that your UV ink is fully cured under the right UV light conditions. Under-curing or over-curing can both affect adhesion, so the intensity of the UV light and the curing time need to be optimized based on the ink and substrate used.
4. Printing Process Optimization
- Proper curing: UV ink requires UV light to cure and bond to the substrate. Ensure the curing unit is properly calibrated to provide the correct dose of UV light for thorough curing. Insufficient curing leads to poor adhesion, while over-curing can cause cracking.
- Optimal print pressure: The pressure applied during the printing process can also affect the ink's adhesion to the substrate. Ensure that the print pressure is set correctly for the specific ink and substrate.
5. Post-Printing Treatments
- Heat treatment or post-curing: Sometimes, applying additional heat to the printed surface after UV curing can improve adhesion, especially on heat-sensitive substrates. This step can help to further bond the ink to the surface.
- Laminate or coating: In certain applications, applying a UV-resistant clear coating or laminate can enhance adhesion, especially for high-wear products like labels or packaging that will be exposed to abrasion or moisture.
6. Environmental Factors
- Temperature and humidity control: Extreme temperatures and high humidity can affect both the printing process and the ink's performance. Make sure the printing environment is stable and controlled to achieve optimal adhesion results.
- Storage conditions: Store printed materials in conditions where they are protected from moisture, extreme temperatures, and dust to ensure the adhesion remains intact after printing.
7. Test and Quality Control
- Conduct adhesion tests: After printing, always test the adhesion quality. Common methods include tape adhesion tests (peel testing), scratch resistance tests, and abrasion testing.
- Monitor ink performance: Keep an eye on ink performance over time, as it may degrade or lose adhesion due to external factors, such as UV exposure or environmental changes.
By following these strategies, you can improve UV ink adhesion and achieve high-quality, durable prints. The exact methods you choose will depend on the specific ink, substrate, and printing technology used.